FMCI Control Centre, Bay 80 Shannon Free Zone, Shannon, Co. Clare for Future Mobility Campus Ireland.
The Renovation of Bay 80 Shannon Freezone comprised of 1,400sqm area for the following rooms:
- 4 Workshops
- Conference Room
- 2 Main Offices
- Control Room
- Co-Working Office
- COO Office
- CEO Office
- Comms Room
- Main Laboratory
- Private Laboratory
- Co- Working Collaboration Space
- Tea Station
- Staff Canteen
- Female & Male WC’s & Showers
- Various Store rooms
Works carried out included demolition, hiring of 3rd parties and project management co-ordination and construction.
Demolition Work
This included Asbestos Removal; Demolition & Alteration Works to be carried out on site. We organised the demolition of the internal walls, existing toilets, all the air conditioning units, all the existing electrical trunking throughout the building has been removed & disposed of.
All Asbestos was removed & disposed of safely by a specialist contractor. We submitted the Air Monitoring Certificate & the Waste Transfer Forms- Shipment of Hazardous Waste Forms to the PSDP for the Safety File for BCAR.
Construction Work
We constructed a new canopy to the front of the building, with new Curtain Walling to the front elevation of the building. We arranged the specialist sub-contractor to complete all the metal studwork throughout the building. We fitted all the plasterboards & taped & jointed the plasterboards. We painted the internal walls. We tiled the bathroom walls, organised the Toilet Cubicles & Sanitary Ware & the Corian Vanity Units.
We constructed a new Substation at the rear of the premises with all associated site works. We installed all the Ducts for Fibre cables & brought them into the building. We reused the external gates & any other existing materials where possible, this is to obviously save money for the client, but also to avoid unnecessary waste on the project & lower our carbon footprint where possible & recycle where possible.
Project Management
We organised the relevant manpower & machinery on site and ensured that the materials were on site before they were needed to avoid any delays. We did this by going through the programme and the critical path and checking the lead times for the materials relevant and ordering as early as possible, even when it meant having to store some materials and having a stock pile in our warehouse which lowered our carbon footprint by reducing the amount of packaging used and also the amount of mileage used by delivery trucks etc. to site. This also helped us to have materials readily available rather than running out of materials, meant that the project ran smoothly and on programme.
All new high spec Mechanical & Electrical services including Air Conditioning, Security & Fire Alarms were installed by reputable contractors. We had previously worked with these Sub-Contractors so we were well aware of their workmanship & qualifications to complete the project on time & on budget. We always confirm the Sub Contractors compliance & capabilities by checking their safety statements, risk assessments, method statements, insurances & staff qualifications & passes before employing them & having a pre-start meeting. The M&E Contractors were in constant contact with the Client’s M&E Engineers to agree submittals etc. We produced all the H&S Site Specific Folders with all our procedures; Construction Safety Plan; RAMS; Site Rules; Method Statements; Tool Box Talks & Site Inductions.
Safety and Compliance
We had all the hard copies of Safe Passes, CSCS tickets & Certificates for all staff & Sub Contractors for ease if HSA called to site. We ensured that all systems were in place to ensure compliance with the construction regulations & all other relevant legislation. We coordinated the daily & weekly inspections of safe working procedures & monitored compliance of contractors & all staff.
Drone Landing Zones
We organised our machines on site to excavate & level the Verti Port Area to house the AAM Hub & Robotic Test Area & install all ducts, create the new car park & Drone Landing Zones & install & fit out the new office cabin on site. We also laid line marking for the Drones to Land & the car parking area. The line marking on this section is vital for the Drones to land in the right spots as to avoid collisions with other Drones.
Ordering Materials
Our combined experience & organisational skills & foresight has meant that we have materials ordered ahead of time where we can. As we have found due to the pandemic that stock of certain materials & transportation has been extremely slow. So, we are always trying to be one step ahead where possible.
Data Managment
All submittals were uploaded onto the Shannon Group Cloud for consideration of the Design Team before approval. We captured all site photos, DOP’s, Data Sheets, Delivery Dockets & Manuals as we go through this project, to avoid any costly delay at completion stage for BCAR.
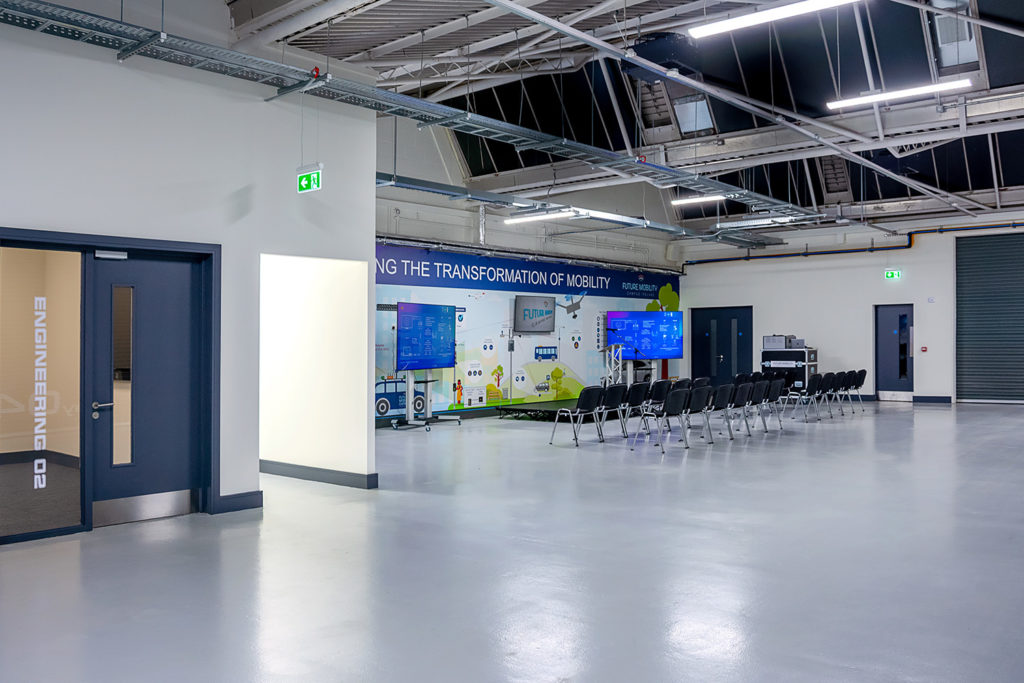

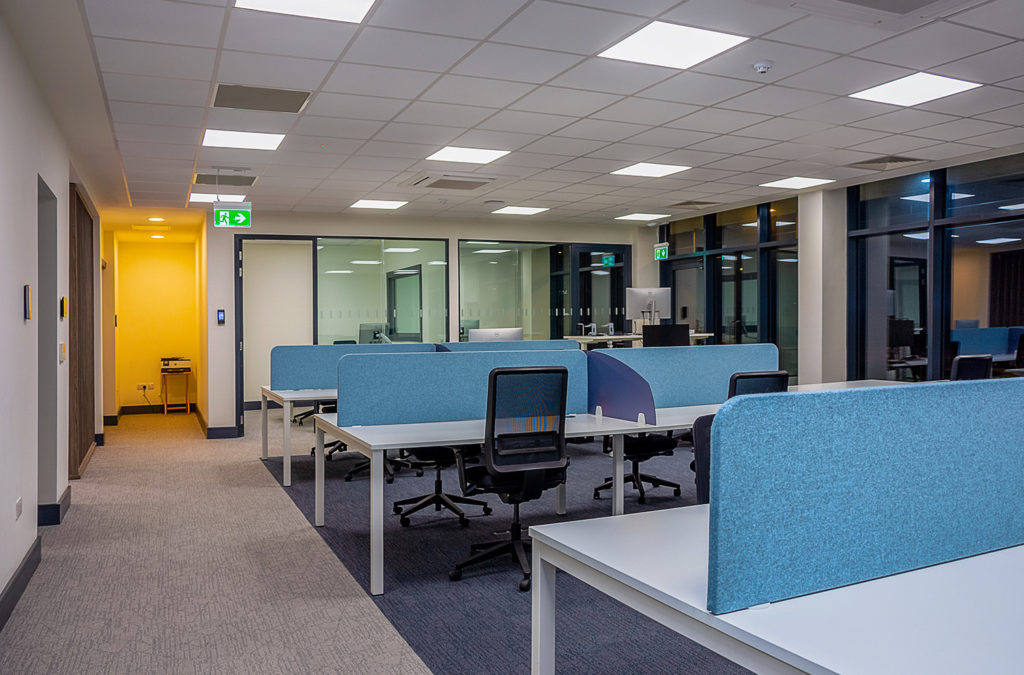
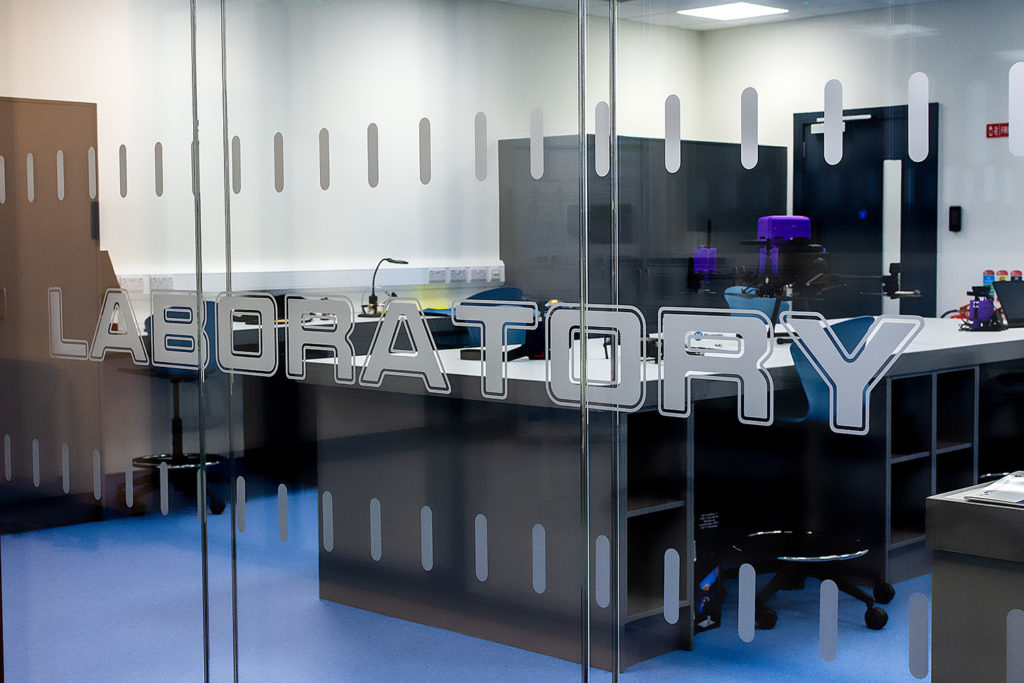
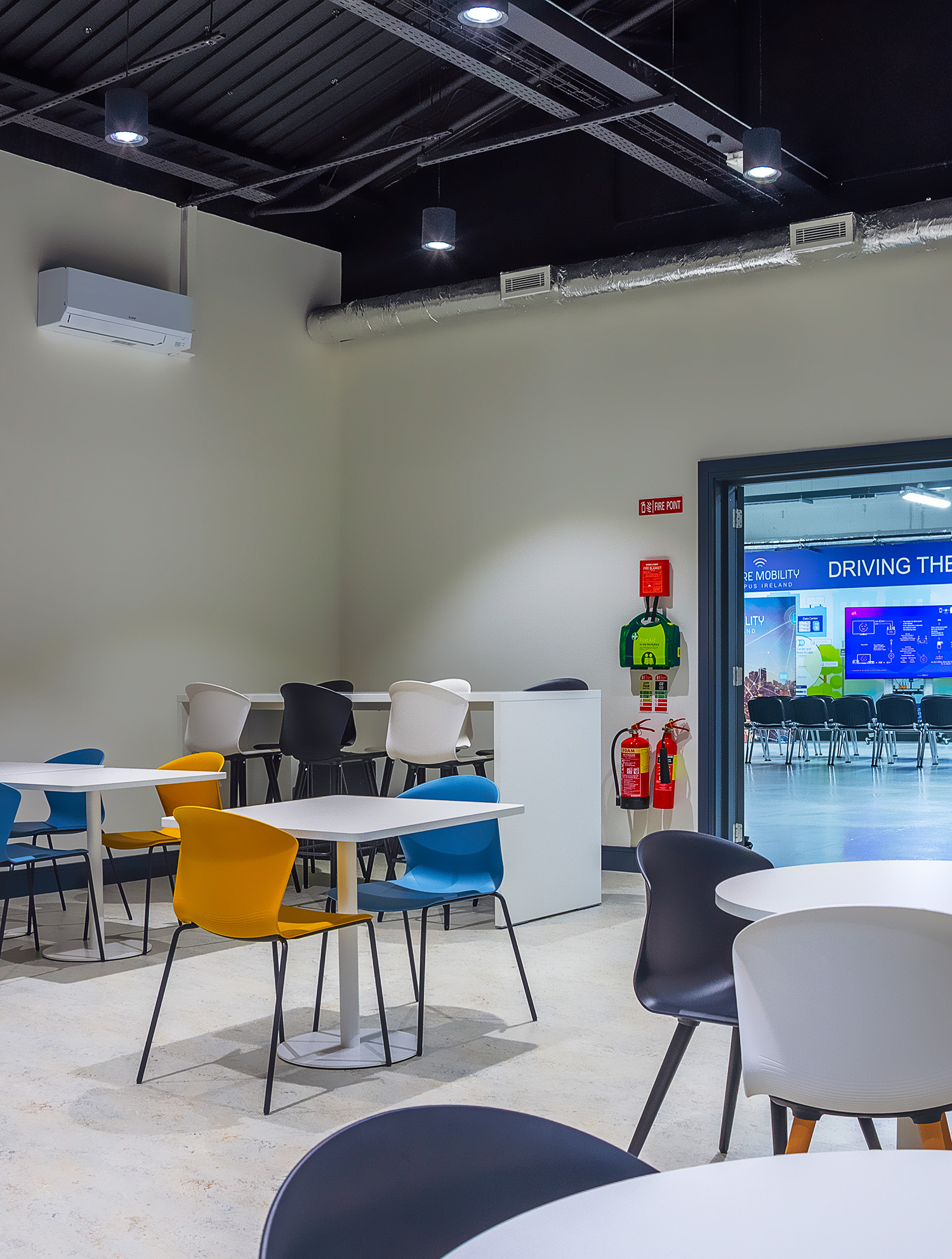